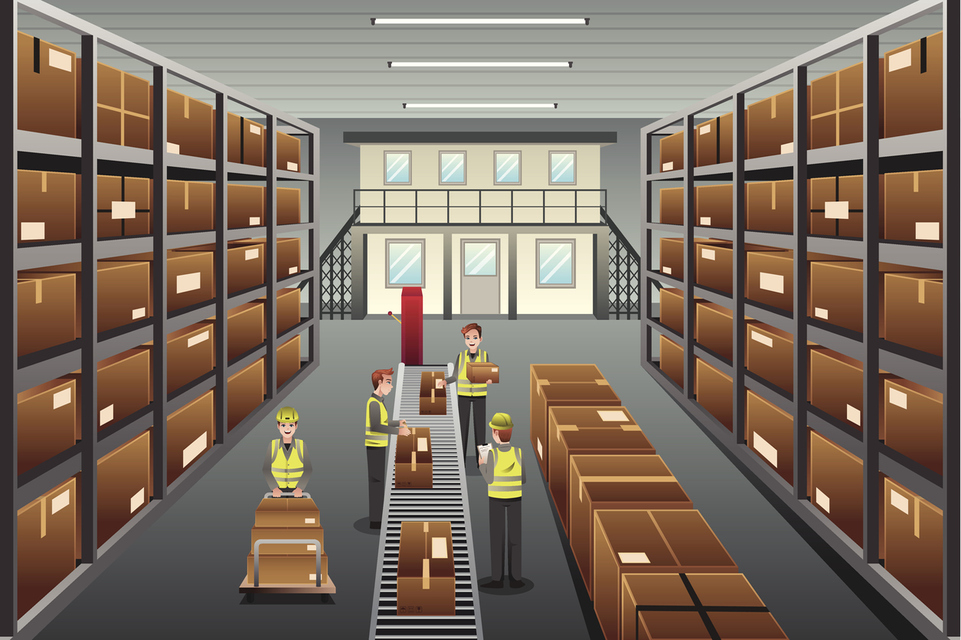
2 áreas en las que puede aumentar la productividad de sus operaciones de almacén
El año pasado, escribimos un artículo con sugerencias para realizar cambios durante el verano, con un enfoque específico para abordar los problemas de seguridad. Con la crisis sanitaria mundial sustituida por nuevas dificultades, este verano puede ser el momento ideal para afrontar algunos retos de productividad. Podría ser una respuesta al declive de los mercados o al incremento de oportunidades de venta, ocasionadas, por ejemplo, por el aumento de las ventas online.
Estas son dos de las áreas en las que podría mejorar la productividad de su almacén:
1. Revise de nuevo la distribución de su almacén
Los seis procesos fundamentales del almacén son la recepción, el depósito, el almacenamiento, la preparación de pedidos, el embalaje y la expedición. Todas y cada una de las áreas ofrecen oportunidades para mejorar la eficiencia, pero la distribución está influenciada por un sinfín de factores. Normalmente, puede tratarse de la acumulación, los tamaños y los volúmenes de la gama de productos, los métodos de trabajo, los tipos de equipos de manipulación de materiales y los tamaños y volúmenes del propio almacén. Sin embargo, hay que tener en cuenta que los cambios en un área pueden afectar al trabajo que se realiza en otras relacionadas, por lo que hay que hacerlos con cuidado.
Para el área de almacenamiento hay muchas soluciones de estanterías diferentes. En otro artículo describimos los tipos de estanterías, sus funciones y sus mejores aplicaciones. Estanterías más altas y pasillos más estrechos combinados con carretillas retráctiles, reducen la superficie de almacén necesaria manteniendo la misma capacidad de almacenamiento. El apilamiento a doble profundidad puede aumentar aún más la densidad, pero requiere una gama de productos más estandarizada, porque se pierde la disponibilidad instantánea de cada palé. Puede explorar formas de combinar el almacenamiento y la preparación de pedidos dentro del mismo sistema de estanterías para sacar el máximo provecho de su inversión.
La zona de embalaje debería estar cerca del final del proceso de preparación de pedidos y conectada con la zona de envío. También puede decidir reorganizar y combinar ambas actividades en una sola sección.
En conclusión, se puede revisar cada proceso. Sin embargo, sólo después de haber trazado el flujo de mercancías actual y haberlo comparado con los anteriores, tendrá la oportunidad de empezar a aplicar dichos cambios. Es una buena idea abordar los seis procesos semana a semana, teniendo en cuenta su interrelación. Una vez completado el proceso de reflexión podrá desarrollar un plan de acción.
2. Reconsidere sus estrategias y recursos de preparación de pedidos
Los cambios en las pautas de los pedidos (más pedidos y más pequeños) podrían ser una buena razón para examinar detenidamente sus operaciones de preparación de pedidos. A grandes rasgos, se pueden dividir los métodos de preparación de pedidos en dos tipos: preparación de pedidos individuales y preparación de pedidos múltiples.
Con la preparación de pedidos individuales, los empleados recogen los pedidos uno a uno, normalmente en palés sobre una transpaleta. Los pedidos grandes con muchas líneas de pedido diferentes se recogen y seleccionan de forma eficiente de esta manera. Pregúntese: ¿los productos proceden de diferentes zonas? Si es así, en lugar de recoger todo el pedido, su recolector podría limitarse a una determinada zona de recogida. Con este método, los recolectores recogen parte del pedido y luego se lo pasan de unos a otros.
Otra opción es recoger los pedidos de diferentes zonas por separado y combinarlos en la zona de envío. A esto lo llamamos consolidación de pedidos. Esto es especialmente útil si los productos de un pedido deben recogerse en una zona de almacén congelada, fría o "seca".
En la preparación de pedidos múltiples, un empleado recoge varios pedidos al mismo tiempo para minimizar las distancias a pie. La preparación de pedidos múltiples puede implementarse de diferentes maneras. Clasificar mientras se recoge significa que los empleados recogen varios pedidos al mismo tiempo y los clasifican directamente en contenedores o cajas. También pueden colocarse directamente dentro del embalaje del envío, lo que se conoce como "pick-in-box" (recoger en caja de envío).
Con el sistema "pick-then-sort" (recoger y clasificar), también llamado "batch picking" (recoger por lotes), se recogen varios pedidos al mismo tiempo y se clasifican posteriormente en pedidos de venta. ¿Cuál es su estrategia actual? ¿Podría aumentar el rendimiento el cambio a uno de estos métodos?
Además de analizar las técnicas, también podría evaluar el equipo actual de manipulación de materiales. El uso de carretillas dedicadas a la preparación de pedidos en lugar de transpaletas o carretillas elevadoras, podría aumentar la producción y mejorar la ergonomía. ¡La reducción de la fatiga y una buena ergonomia es algo que apreciarán sus empleados!
- Medidas prácticas
- Prepare una reunión conjunta con sus proveedores de estanterías y de manipulación de materiales para discutir su nuevo plan de flujo de mercancías
- Pida a sus empleados que contribuyan al plan de cambio con sus propias sugerencias
- Desarrolle un plan detallado para que el cambio sea práctico y viable